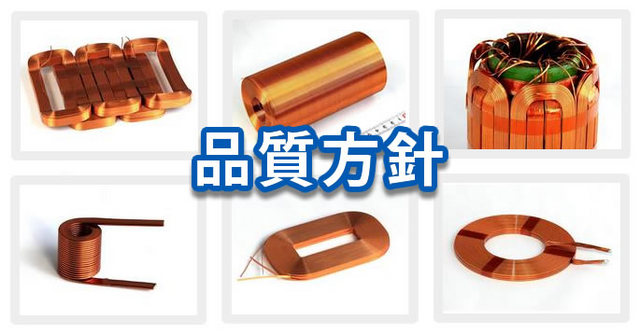
平成24年1月 ISOQARによってISO9001:2008の認証登録されました。 2023年7月 ISO9001:2015更新
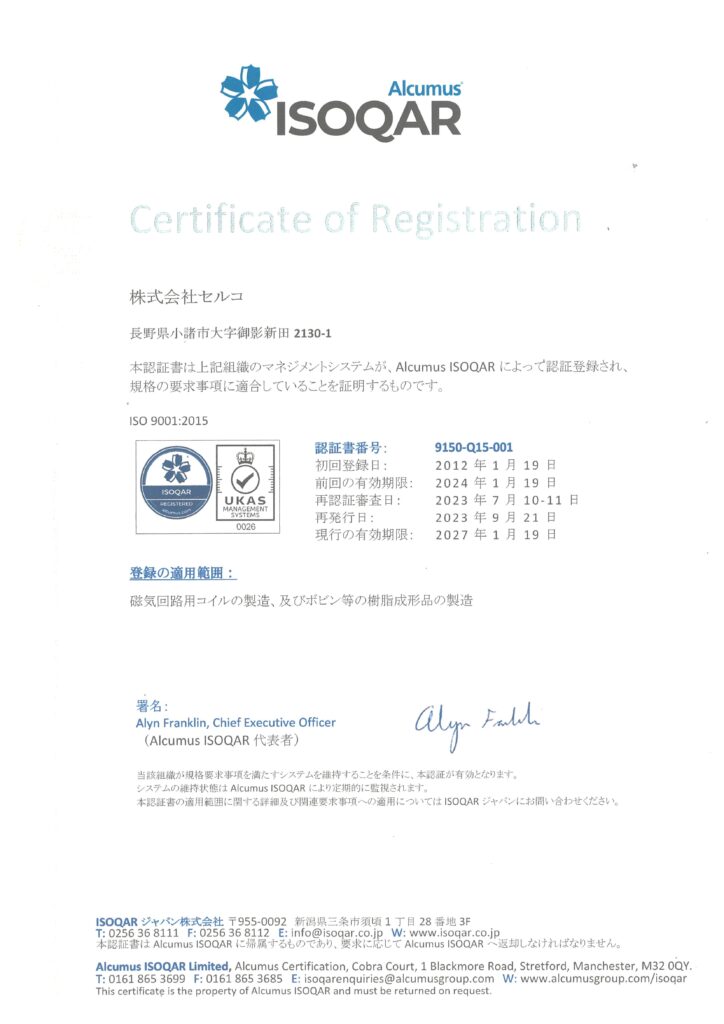
当社では、ここ十数年来毎日「不良解析」をおこなっています。不良解析とはその日に生産工程で赤箱、黄箱に省いたモノを製造の担当者・管理者が全て机に並べ、廃棄するもの、手直しするもの、特採をお願いするもの等を区分けすると同時に不良の原因を徹底追及し、何らかの改善につなげております。
製造上の問題点は、実にこの省いたモノの中に殆んど含まれております。
本当にきちっと解析し、それぞれに改善を施して行けば、製造上の問題点は殆ど無くなるはずです。
当社が完璧にできているか?と言いますと、未だ完璧とは言えません。
これを完璧にやり遂げるためには、担当者、管理者のスキルの問題とパワフルな実行力、行動力が必要です。しかし、やり続けていることによって、間違いなく徐々にではありますが良い方向へ向かっているのは確かです。
次の「工程内造り込み」のための手段は、「巡回検査」です。
これは、品質保証の担当と責任者が毎日一回現場を回り、品質の確認をしたり、ちょっとしたことは、その場で注意、改善もします。毎日内部監査をしているようなものですね。
これも既に始めて10数年、最近は、かなりその見回りの”質“も上がって来て、”転ばぬ先の杖“的な指摘が多くなってきており、非常に良い傾向です。
それでも、未だ「なんでこんな不良が出るんだ?」と言うような、」ポカミス的な不良が出ます。
その殆どは、「新人作業者」によるものです。いわゆる4M変動時です。
先般も、お客様の工程に影響が出るような不良が勃発し大変な状態になり、落ち着いたところでお詫びに伺ったら、逆に対応が非常に良かったと言って褒められました。
あまり自慢にはなりませんが、このような場合、特に私が「こうしろ、ああしろ」と指示することはありません。当社の製造、品質の各担当・責任者は、自分の責任において必死になってリカバリーしようとします。それが、今回もお客様の目には、良く映ったということでしょう。
いずれにしろ、当社の目標はZDです。ゼロ・ディフェクト(無欠点)にするためには、やはり工程の中で様々な問題を潰す必要があります。完璧を目指すのであれば、不良が出るような工程を完璧に無くすこと・・・
すなわち、お客様の設計にまで話が及ぶ可能性もあります。
あるお客様で不良が多発し、当社に製造依頼が来ました。私が見たら、結線位置が非常に危険なところにあったため、これは、もっと安全なところで結線すればいいと提案したら、それ以降、フンもスンも無くなってしまいましたが、設計する技術者が“モノ造り”をやらなくなるとこのような簡単な問題で、不良を出し続けるようなことが往々にしてあるのです。
品質は「造り込み」によって向上します。また生産技術も同時に造り込みによってスキルアップします。
私達のモノ造りは、世界の中でも最高峰を行く“日本のモノ造り”を基盤とした本物のモノ造りを目指すものです。